Are automatic bagging machines the right solution for you?
Reach new levels of efficiency, increase output, and realize more productivity with a fully integrated high-performance bagging machine from STATEC BINDER.
We’ve been meeting our customers’ bag machine needs with safety, quality, and reliability as the exclusive U.S. distributor for STATEC BINDER since 2018.
Whether you’re replacing an old system or considering your first automated bagging machine or integrated bagging line, Columbia/Okura can custom engineer a solution to fit your space and your needs as your single-source, US-based, OEM provider.
STATEC BINDER open-mouth and FFS bagging machines are flexible, rugged, and precisely engineered machines that allow you to free up space in your packaging area, ensure accurate bag placement, and keep up with customer demand.
Let our experienced team help you choose the appropriate bagging machines for your operations.
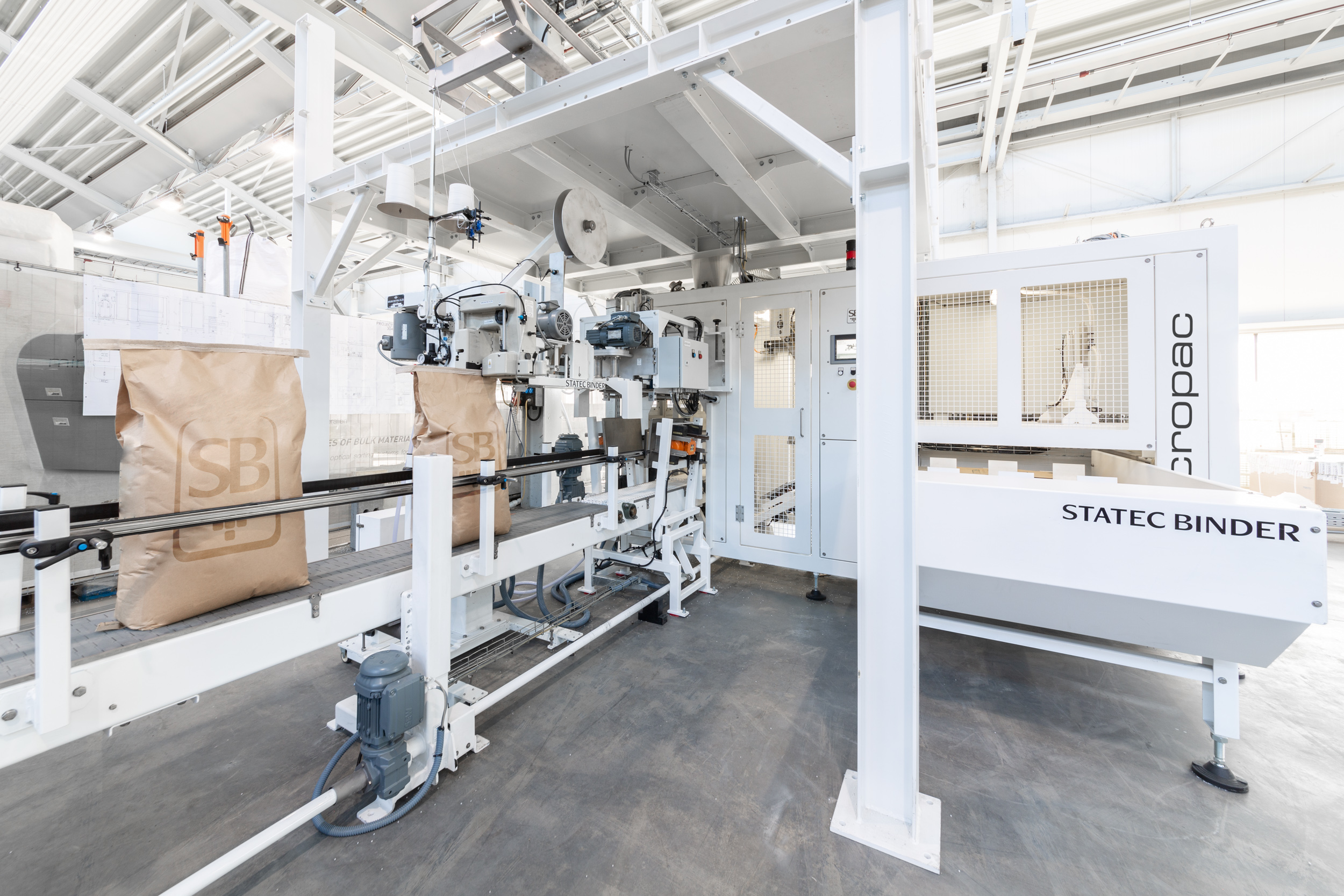
OUR PARTNERSHIP WITH STATEC BINDER
For more than 45 years, Austrian-based STATEC BINDER has set the standard in high-speed fully automatic bagging technology. With over 1900 systems installed around the globe, the company has earned a reputation for engineering excellence, dependable performance, and forward-thinking innovation. Its versatile, high-quality packaging solutions are trusted across a broad spectrum of industries and applications.
As industry leaders, Columbia/Okura and STATEC BINDER are united by a customer-first approach and a shared commitment to delivering reliable custom-engineered solutions to meet manufacturers’ demanding requirements.
Need Bagging Machines Outside the USA?
Contact STATEC BINDER for global solutions. Complete the contact form on their website to connect with a representative in your region.
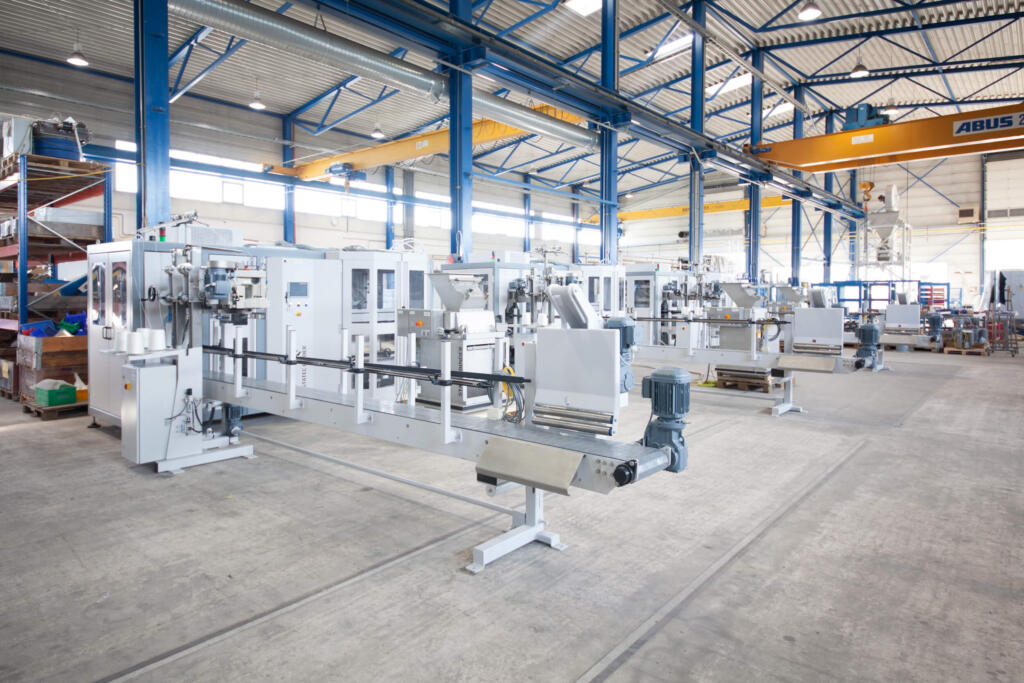
PRINCIPAC
The PRINCIPAC is a fully automatic, high-performance bagging machine for open-mouth bags—capable of filling up to 2000 bags per hour, making it one of the fastest systems in the world. Engineered for high flexibility, it efficiently packs free-flowing bulk materials or, with optional dustproof equipment, powdery products into 10–50 kg pillow or gusseted bags. It supports woven PP, PE, and paper materials and can be partially or entirely constructed of stainless steel to meet hygiene or corrosion resistance requirements. Its reliability, compact design, and flexible features make it a powerful solution for achieving higher throughput, long-term performance, and custom integration. The available Twin Version features two bag placers and filling stations in one machine to bag up to 2400 bags per hour.
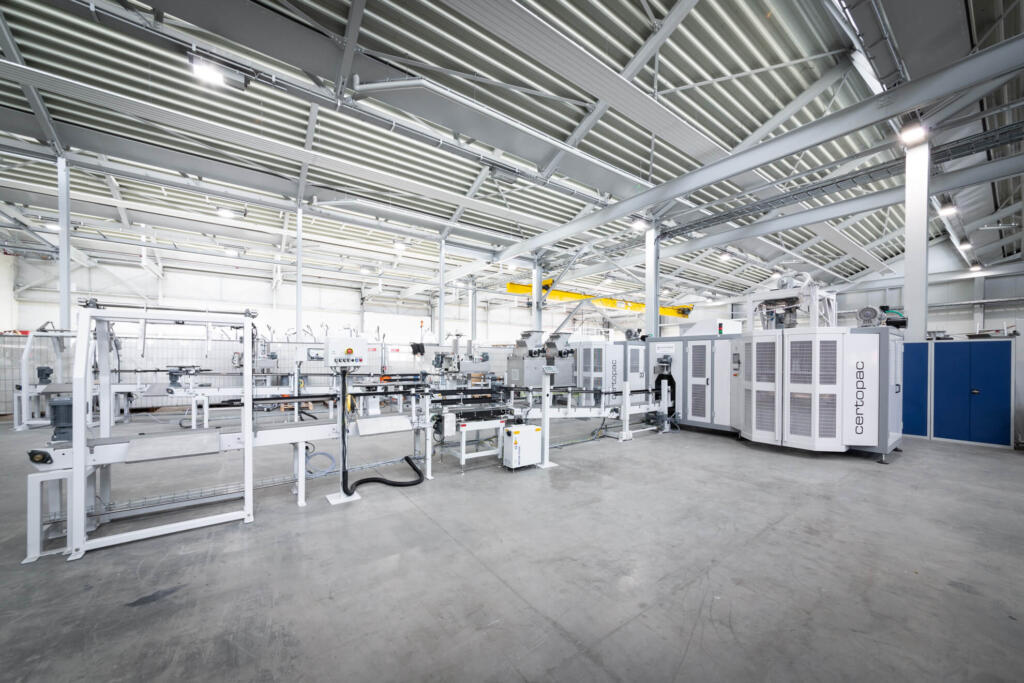
CERTOPAC
Advanced engineering and innovation make the CERTOPAC an exceptionally reliable market leader. This fully automatic high-speed bagging machine is built for demanding industrial environments. With capacity up to 1500 open-mouth or gusset bags per hour, it handles a wide range of free-flowing materials—from fertilizer and plastic pellets to sugar, pet food, beans, and rice—in bags from 5 to 80 kg. Its modular, compact design ensures smooth integration even in tight spaces, while its stainless steel options meet hygienic standards for food-grade or powder applications. Choose from standard, S, or L models with rotating or push bag magazines to suit different bag sizes.
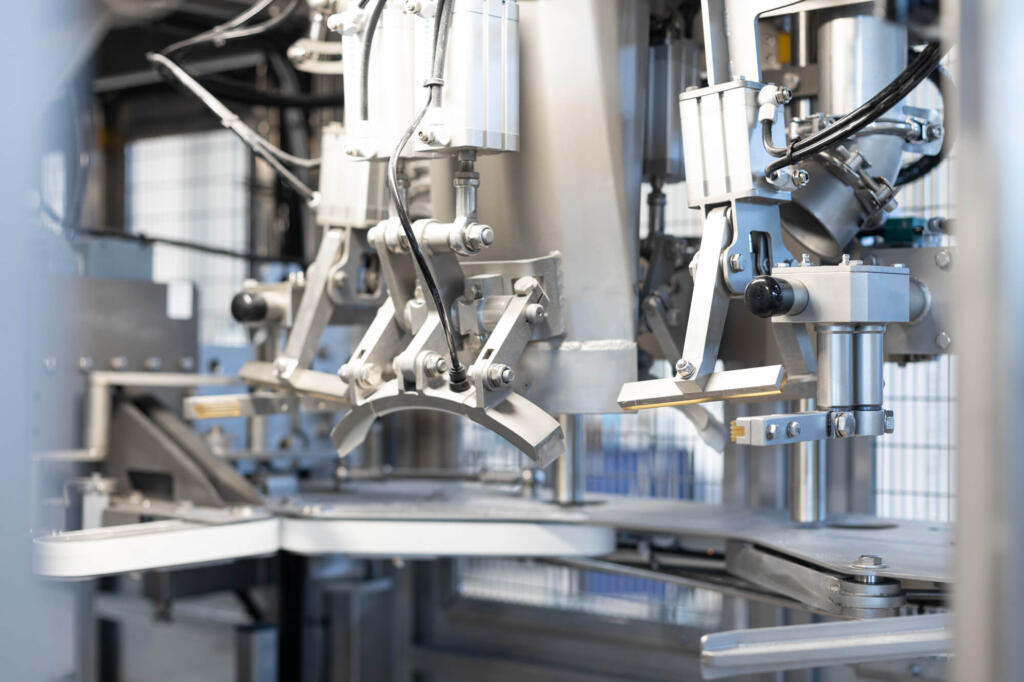
ACROPAC
Compact, reliable, and highly adaptable, the ACROPAC is a fully automatic bagging machine designed for smaller operations or those taking their first step into automation. With a capacity of up to 600 open-mouth bags per hour, it handles free-flowing bulk goods like fertilizer, food, and animal feed with precision. This flexible system supports 10–50 kg pillow and gusseted bags made of woven PP, PE, or paper. Built with quality materials for long-term performance, it features a compact footprint, easy-access design, and low maintenance demands. This is an efficient, space-saving solution that keeps labor and operating costs in check while increasing throughput.
Custom Bagging Solutions to Meet Your Needs
Hear from the packaging manager of Barrett Pet Food speaking to the impact we’ve had on their family-owned small business. With an integrated line including a palletizing robot and a PRINCIPAC bagging machine, they saw a 15-66% increase in productivity on their bag fills. Let us introduce you to the variety, precision, and technology of these precisely engineered bag machines.
Get Started on Your Growth
Ready to meet your production goals? Let us design a completely integrated end-of-line system that’s right for your business. We’ll even help you develop a comprehensive plan and business case to justify the investment.
About Us
For nearly 30 years, we’ve been helping our customers become more competitive, cost-effective, and productive in a fast-changing world.
Our Partnership Promise
From installation to 24/7 technical trouble-shooting, you’re getting a complete support and service team you can always rely on.
Find answers to common questions about automatic bagging machines
How do automatic bagging machines work?
Bagging machines are designed to automatically fill bags with bulk solid products like granules, powder, flakes, and pellets. Bags feed into the filler from a bag magazine. The machine opens them, fills them, and seals them, producing uniformly filled packages. These machines handle open-mouth bags for applications between small, 5 kg bags to jumbo, 80 kg bags. Bag machines integrate with palletizing equipment, including conveyors and accessories, to build pallets of uniformly filled bags for shipping and storage.
What model of automatic bagging machine do I need?
Let our experts help you figure that out. Automatic open-mouth bagging machines have several configurations to allow for customized layout needs. Plus, every system is optimized to meet the specific production environment. Columbia/Okura Application Engineers are experienced and skilled at specifying bagging machines and accessories. They evaluate your products and bags to find the machine that best suits your production needs.
In addition to open-mouth bagging machines featured above, STATEC BINDER offers an exceptional line of fully automatic form-fill-seal (FFS) bagging machines. These include the high-capacity System-T, which produces bags from a PE tube, and the System-F, which produces bags from rolls of flat PE film.
We work closely with our customers to determine your unique requirements, and can demonstrate customer-provided samples on our equipment. Then we recommend the best overall bagging solution
What products are STATEC BINDER automatic bagging machines suitable for?
STATEC BINDER bagging machines are suitable for most free-flowing to moderately free-flowing products. Around the world, STATEC BINDER bagging machines automate packaging for a wide variety of industries, from food and agriculture to chemical, minerals, and fuels.
Common products using open-mouth bagging machines are rice, sugar, salt, beans, corn, fertilizer, seeds, animal feeds, and pet food.
What types of bags will your automatic open-mouth bagging machines handle?
STATEC BINDER bagging machines are compatible with paper, PE, and WovenPoly (laminated or non-laminated) bags.
Can Columbia/Okura provide a complete system?
Yes, Columbia/Okura designs, integrates, and commissions end-of-line robotic palletizing solutions. We can supply upstream and downstream components, including feed bins with net weigh scales and stretch wrapping.
STATEC BINDER bagging machines have a variety of options available. Depending on the model, these include:
- Stainless steel execution
- Bag top de-aeration unit
- Dustproof filling spout
- Wash-down execution
- Bag vibration device
- FFS-Combi version
- Evacuation lance
- ATEX execution
- Bag labelling
- Washing & drying