Reconfiguring the palletizing system to meet customer needs
Today, manufacturers must adapt their operations to work with various package styles and configurations to meet their customers’ needs. Michigan Sugar Company is no exception.
The Bay City, MI-headquartered cooperative is made up of nearly 900 grower-owners. It sells its sugar to industrial, commercial, and retail customers under the Pioneer and Big Chief brands. In 2010, a request from McDonald’s for 4-lb bags of sugar packed in overwrapped trays led the company to replace a mechanical palletizer with a robotic system from Columbia/Okura. In 2018, Michigan Sugar installed a second Columbia/Okura system at its Sebewaing facility, this time in response to a demand for retail display pallets, where individual, unbundled bags of sugar are placed on pallets in a range of patterns, according to customer requirements. “For the display pallet experience, you need the total flexibility of a robot,” says Michigan Sugar Director of Engineering Jim Martin.
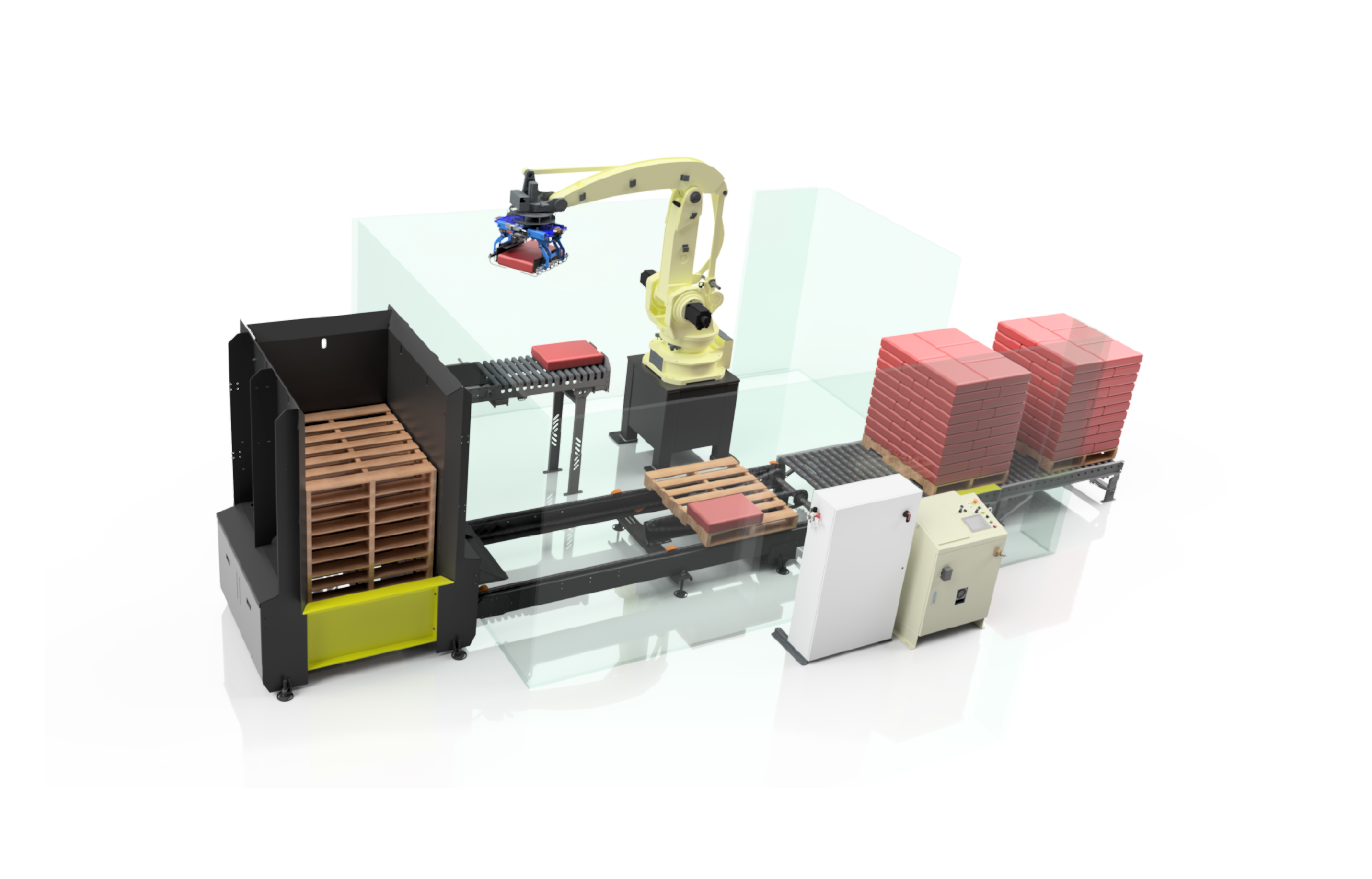
Choosing flexibility, reliability, and ROI of dynaPAL™
As it evaluated the machinery and supplier best suited for the new application, Martin explains, “Of course, Columbia/Okura had the advantage, since we had experience with them, and they performed very well for us in the past. So, there was no question mark with them as far as knowing what we’d get for the money.”
What they got was a dynaPAL™ high-speed robotic palletizing system. The new robotic palletizing system can stack whole and half pallets at speeds to 10 pallets per hour—“which,” Martin says, “is not lightning fast, but it’s reliable, and it just keeps on working.”
SEE THE DYNAPAL™ PALLETIZING SYSTEM AT WORK FOR MICHIGAN SUGAR.
"You...tell it what your end product will be, and the robot figures it all out from there. It’s super simple to learn."
Jim Martin, Director of Engineering at Michigan Sugar
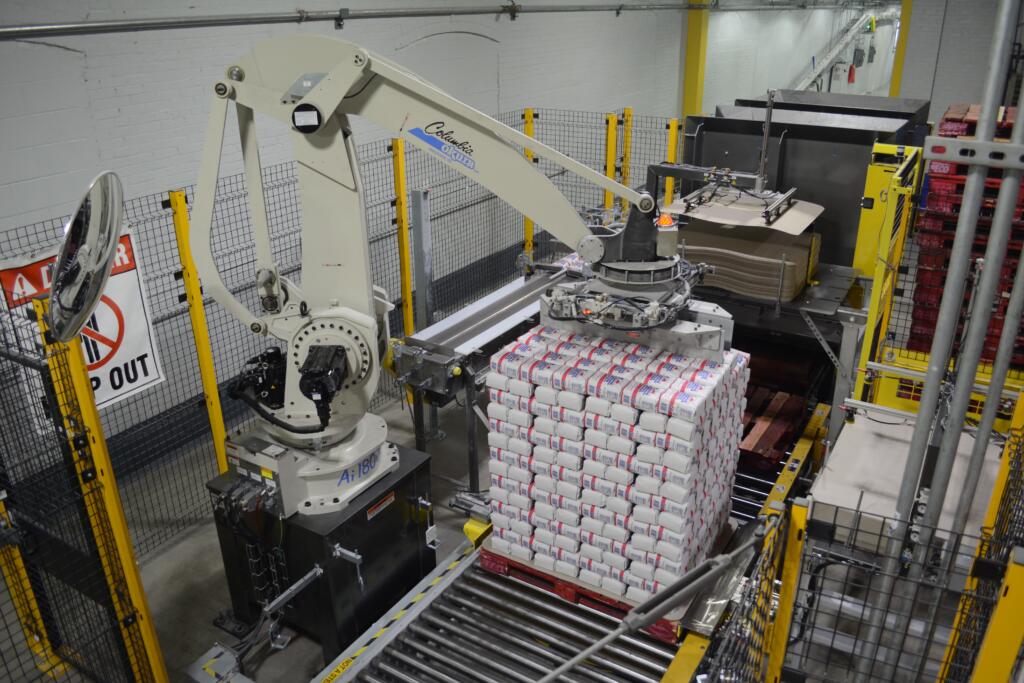
Custom-engineered solutions
Michigan Sugar uses the dynaPAL™ with four-pound bags of sugar to palletize in patterns determined by the retailer. One of the improvements Columbia/Okura made on the design of the robot was to remove the third paddle from the end-of-arm tool responsible for holding the bags securely during picking and placing. This adaptation provided two benefits, explains Martin. “First, when you get rid of that intermediate paddle, when it comes time to lift the robot away from the pallet, you don’t get any rub against the bags that would cause them to tweak. Second, it allows you to pack the bags side-by-side, very close together, which is very important when you’re creating interlocking rows. You get a much tighter pallet.”
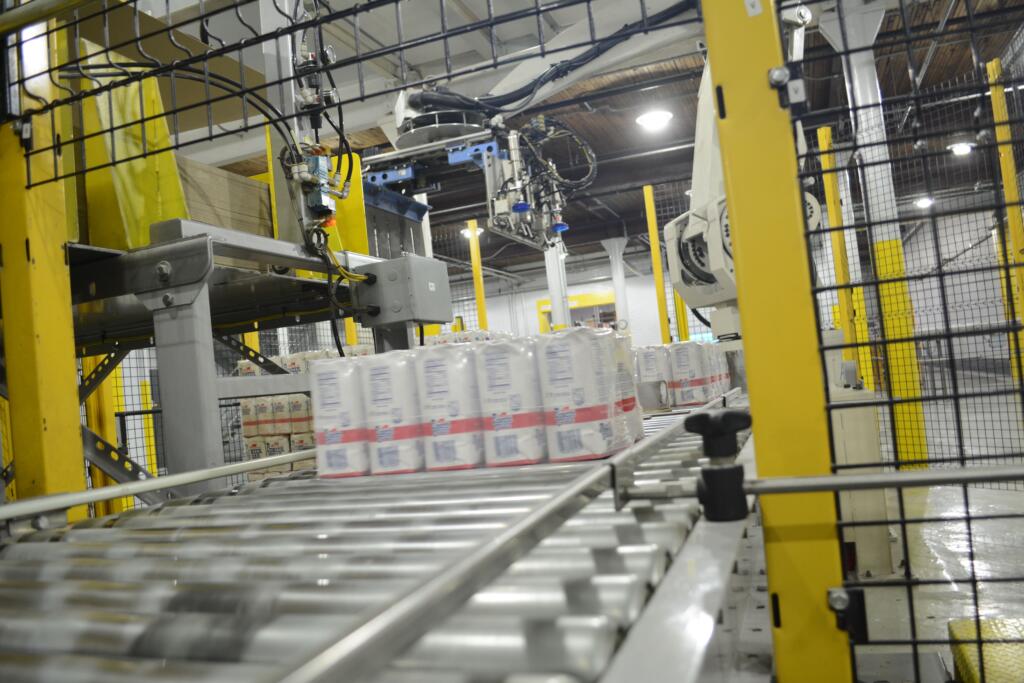
Improved efficiency with ease of use
Another improvement to the system is its ability to create half pallets as if they are whole ones—saving a lot of time. “That’s one of the big things that Columbia did for us,” says Martin. “They found a way to do the cross picks across two pallets as if they are a whole one and then split them apart. We didn’t think that was possible, but they showed us how.”
Michigan Sugar learned from its experience with the first Columbia/Okura robot that programming the dynaPAL™ is very easy. A touchscreen interface offers user-pattern programming and easy operation. “The robot allows us to tweak and adjust the running conditions as we change the product and the bags we get from our suppliers,” says Contracted Project Engineer Robert Hite.
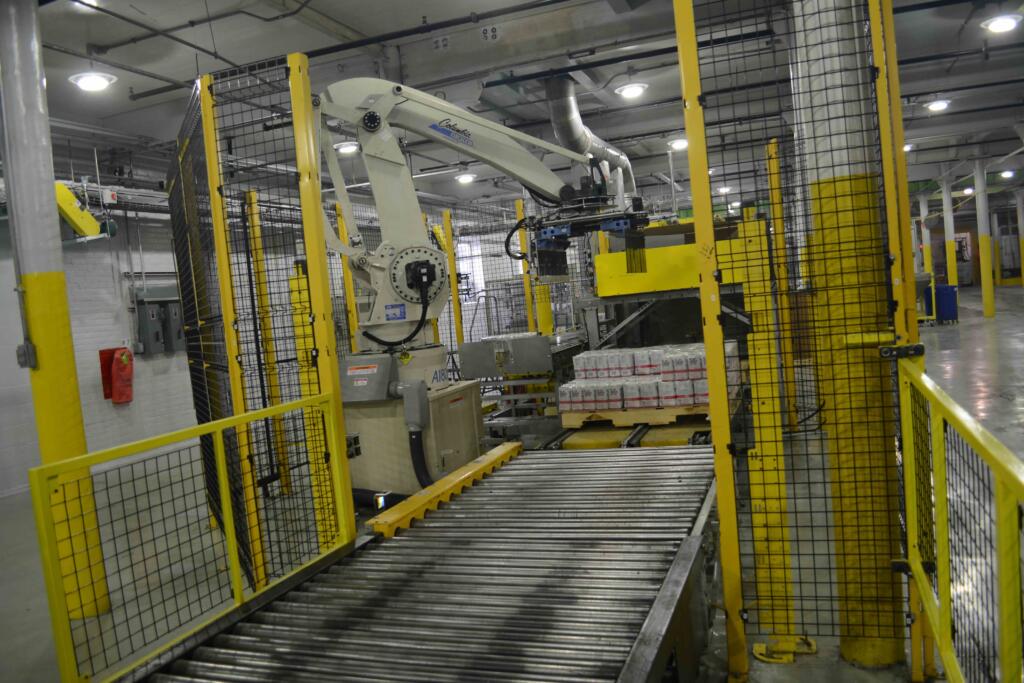
The workforce benefits from ‘hiGH-quality equipment’
Michigan Sugar sent a team of people from its plant, including mechanics and electricians, to participate in the Factory Acceptance Tests at Columbia/Okura’s facility. Having employee expertise in the palletizers has proven a positive experience for the plant overall. Says Michigan Sugar Executive Vice President Jim Ruhlman, “At Michigan Sugar Company, we like to say our sugar is ‘Packed with Pride,’ and the morale boost of creating a state-of-the-art pallet is huge out in Sebewaing. There is an inherent benefit for the workforce when you have high-quality equipment putting out a high-quality product.”
Automation challenges solved
- Adapting to new packaging types with minimal downtime
- Durability and reliability
- Quality of pallet loads improved from hand-stacking
Key value drivers
- User-friendly interface for pattern changes
- Improved employee morale from state-of-the-art pallet-building and access to innovative equipment
- Meeting retail customers’ needs