Transforming end-of-line operations for growth
Supreme Rice first began investing in automation to keep up with demand for its bulk products. Founded in 1936, Supreme Rice is the largest rice milling operation in the state of Louisiana. From its 50,000-square-foot mill in Crowley, the company processes over a billion pounds of rice every year and exports to over 50 countries.
But when Supreme Rice decided to expand its sales to the retail channel in 2013, it faced a new dilemma: how to pack, bundle, and distribute its product for grocery store shelves.
“There were obviously a lot of challenges that we hadn’t faced previously in selling rice in bulk, in 50-pound bags and 100-pound bags,” explains Henry Helo, Supreme Rice’s sales director. “It’s very different to do that on a smaller scale, in 1-pound bags up to 20-pound bags. The human is very limited in how fast they can stack a pallet. At that time, we realized that if we did not develop some sort of automation, we would just not be able to keep up with the demand.”
Industry
Food and beverage
EMPLOYEES
150+
Robot
dynaPAL™ System
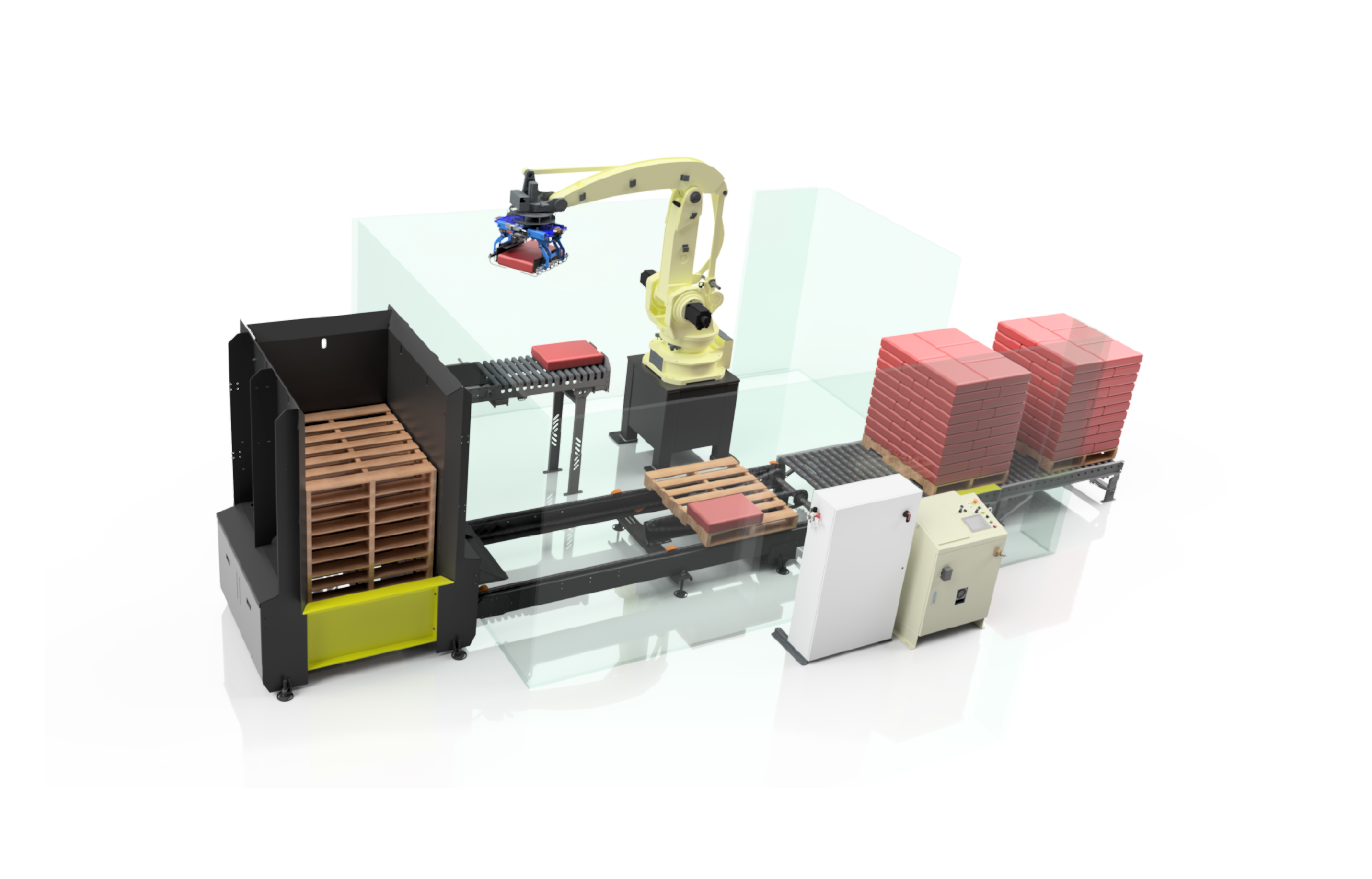
Overcoming a labor shortage with automation
Nicknamed “the Rice Capital of the World,” for having milled more rice than any other city in the U.S., Crowley, Louisiana is a humid place most of the year. The surrounding 657 square miles of Acadia Parish have long, hot summers and mild winters. The subtropical climate and low-lying plains provide a long growing season and topography that’s ideal for rice cultivation—but not for finding enough workers who can handle heavy physical labor.
Supreme Rice knew that to reach its goals of doubling production and penetrating the national retail market, it needed to rely less on the very limited pool of people in the local area who could handle loading bulk bags into trucks or on pallets.
“Historically, we have struggled to get workers to show up consistently,” explains Helo. “Their jobs have been a lot of hard manual labor. Automation would allow us to increase production without struggling to find labor, a consistent problem in our industry and location.”
CHECK OUT THE DYNAPAL™ PALLETIZING SYSTEM AT WORK FOR SUPREME RICE
"We went from 5, 8 employees to 60 on a daily basis. And what we've found is with the robots and the technology we have in packing, we upgraded our people."
Brad Richard, Operations Manager, Supreme Rice
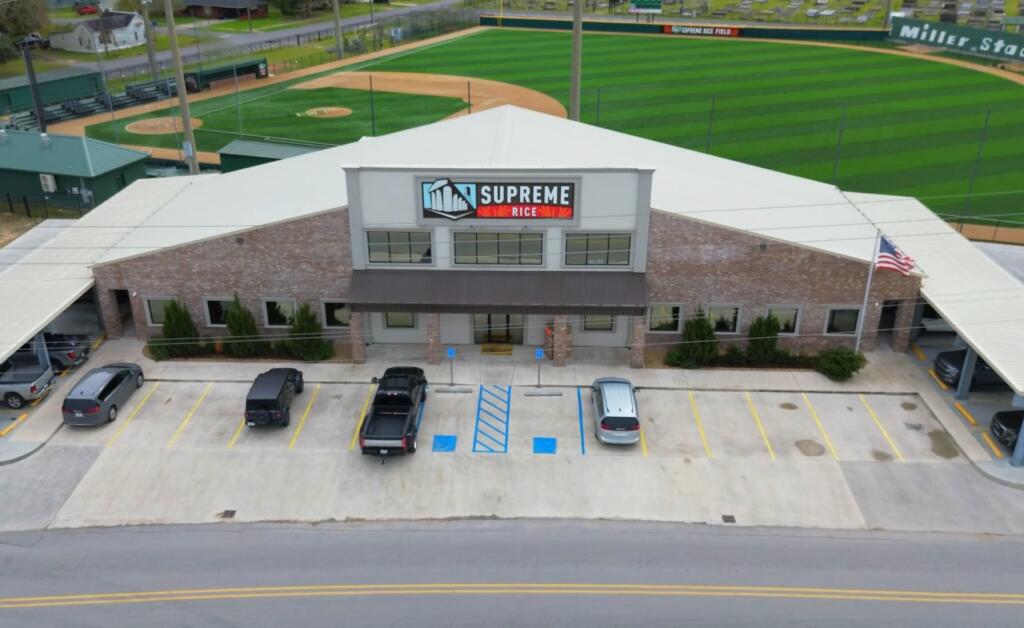
Automating the legacy line before expanding
To find out how other rice mills used automation to improve production efficiency and increase output, the company owner and director of operations set out on an exploratory mission.
“We traveled to a couple of California rice mills, and they had Columbia/Okura robots and they gave very good reviews of Columbia/Okura,” says Operation Manager Brad Richard. The referrals led to a visit to the company’s headquarters. Helo says it was not only the similarity in size and businesses served that led them to trust Columbia/Okura with its automation, but notably, “the time and attention they took to understand our needs and ensure we understood the process.”
In 2016, Supreme Rice installed the dynaPAL™ system that included a robotic palletizing robot, in feed and discharge conveyors and integrated stretch wrapper.
“The goal at this time was to ensure we could continue to produce bulk bags that would be shipped abroad while we explored the new venture of packaging in smaller quantities for consumers,” explains Helo.
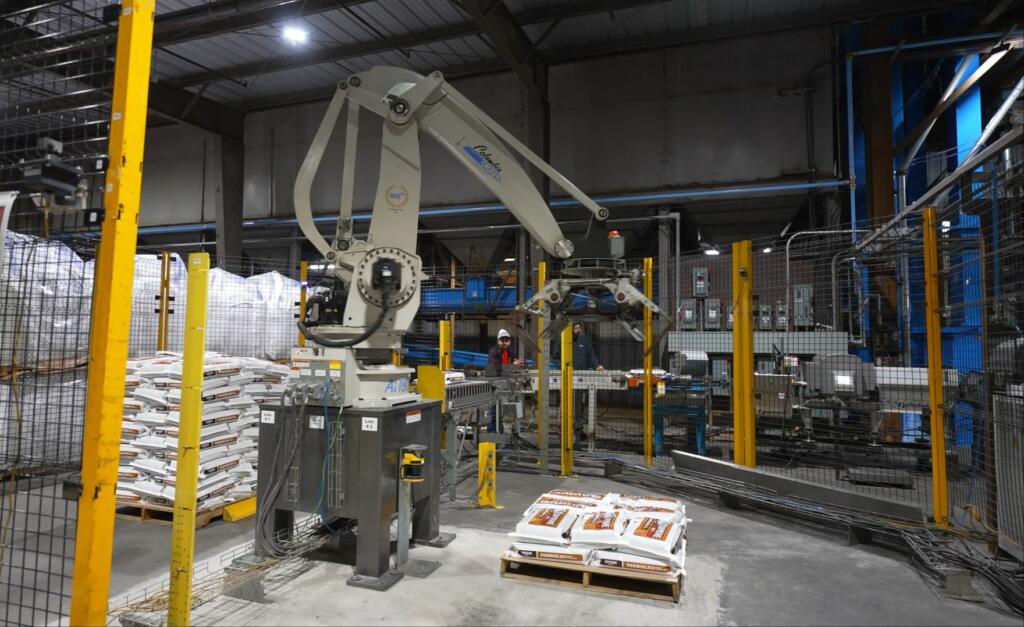
Investing in automation proved an investment in employees
People are a priority for Supreme Rice, and the company leaders are visibly proud and outspoken about the impact the dynaPAL™ has had in not only growing its workforce but also upgrading their work.
This outcome was a bit of a surprise. “We thought we’d have to cut so many jobs to pay for it,” explains Richard. “But it was just the opposite. With the increase of production, we actually increased people. But it was more of people driving forklifts. We have guys watching in quality control more than doing physical labor. It changed the way we do business.”
Helo agrees. “Workers who have worked with us year after year have been given the opportunity to upskill, learning how to operate the equipment, trouble shooting, and learning the mechanics. It has been great to see our workforce numbers grow, while we have also supported them with their own career growth.”
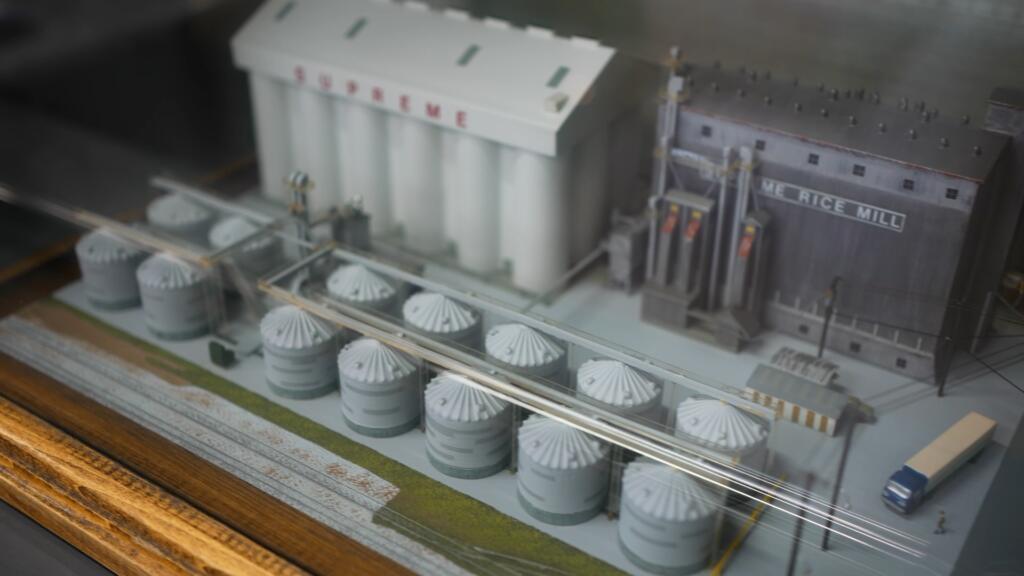
‘This growth wouldn’t be possible without automation’
After introducing the dynaPAL™, Supreme Rice has more than doubled production. Helo credits its Columbia/Okura partnership with the business’s ability to grow with the right processing facilities and equipment. Thanks to the investment in automation, Supreme Rice opened seven new loading docks in late 2024. From sending out two truckloads a day before the dynaPAL™ installation, the company now sends out 50-60 truckloads a day.
Riding high on its successful growth, Supreme Rice is setting its sights on further expansion in the future. At the end of 2024, the company began to make plans to tear down one of its milling facilities and rebuild with the goal to triple production. Says Richard, “That wouldn’t be possible without automation and partners like Columbia/Okura.”
Automation challenges solved:
- Increase output and improve efficiency
- Overcome shortage of available workers and improve workplace safety
- Complete integration and introduction of new packaging lines
Key value drivers:
- Custom-engineered solutions that meet business’s growth goals
- Create more skilled jobs and support employees’ career growth and quality of life
- Expand into national market with new product line
FIND OUT MORE ABOUT OUR ROBOTIC PALLETIZING SYSTEMS
Learn about the dynaPAL™ palletizing systems.