The business transformation
Inspiring joy with wholesome foods. That’s the mantra at Bob’s Red Mill in Milwaukie, Oregon. The company has grown from humble beginnings in 1978, when Bob Moore and his wife Charlee first started milling whole grain flours and cereals, to an approximately 800,000 square-foot large facility that employs 700+ workers, making more than 200 different products distributed across the globe.
“Our vision is to double the number of people eating Bob’s Red Mill by 2030. Automation will help us reach that goal,” says Nick Chow, Engineering and Fabrication Manager at Bob’s Red Mill, who started deploying larger industrial palletizing robots as the manual labor market dwindled during COVID. A solution that worked for the big production lines, but did not fit into smaller lines. “We wanted a robot that could operate much closer to operators in more confined spaces,” explains the engineering manager.
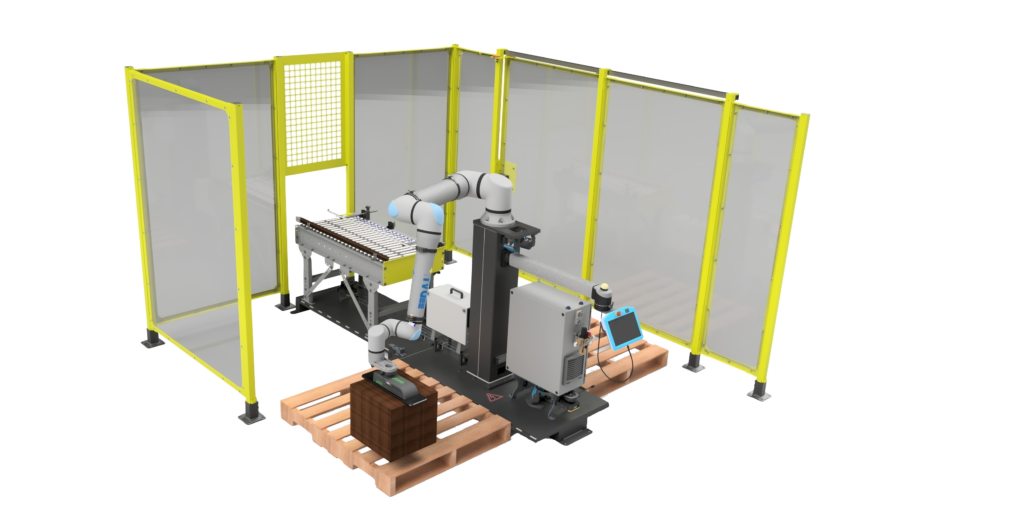
Looking for a larger cobot
But when Bob’s Red Mill researched the cobot market, the company was unable to find a solution that met the reach, payload and speed requirements of their palletizing cell – until Nick Chow heard from Universal Robots’ partner Columbia/Okura that the company was working on incorporating the UR20 cobot into their turnkey palletizer; the miniPAL® 20. “We had already worked with Bob’s Red Mill, deploying larger robots, and knew the UR20 would be a perfect fit for their smaller cells,” says inside sales specialist at Columbia/Okura, Parker Morris-Pinson.
WATCH HOW BOB’S RED MILL DEPLOYED THE UR20 COBOT-POWERED MINIPAL 20 PALLETIZER FROM COLUMBIA/OKURA.
"We have been eyeing UR cobots for a long time; I liked all the little case studies they do, whether it's loading CNC machines or using them in applications like ours. We appreciate the simplicity, their track record and the out-of-the-box features. We tried another cobot that was too sluggish to keep up with our production rate, so we kept hoping that UR would develop a bigger, faster cobot like this."
Nick Chow
How they did it
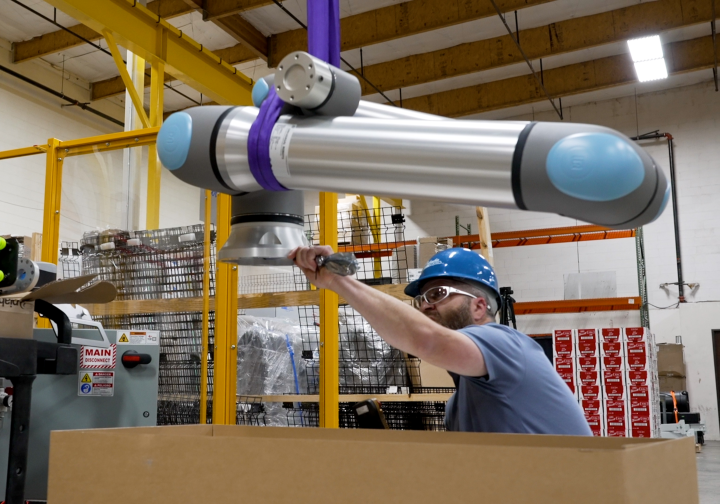
Quick-to-deploy miniPAL+® keeps up with production rates
Columbia/Okura’s new miniPAL® 20 is a turnkey palletizing system that includes the UR20 cobot arm, safety area scanners, radar, guarding, built in pallet jack pockets, the CPT vacuum gripper from PIAB, and PALLY; palletizing software from Rocketfarm, certified through Universal Robots’ UR+ platform for UR cobots. When the miniPAL+ hit the production floor at Bob’s Red Mill, it just took a couple of hours to unbox and bolt everything together.
“Compared to the week-long installation of a traditional industrial robot, the UR20 implementation is much quicker,” remarks Chow, who will have the miniPAL 20 handle up to 14 cases a minute. “Our current production requires 7-8 cases per minute, but we are aiming for a 10-12 case rate, so with 14-case-per-minute capacity, we can also account for the time it takes to add slip sheets in between each layer and allow the cobot to catch up if needed,” he says, adding how the UR20’s 20kg (44.1lbs) payload enables the company to double-pick boxes that each weigh between 4-10lbs.
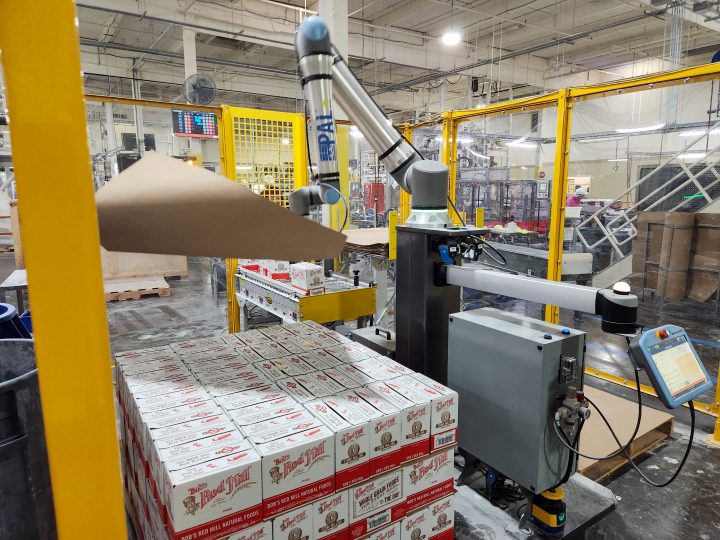
Eliminates need for a 7th axis
Though he had expected a bigger cobot, Nick Chow was taken aback when he first looked up at the outstretched UR20 arm, delivering a 1750mm (68.9in) reach capacity. “I was surprised! It’s a hefty cobot that gave us confidence it would be robust enough to keep up,” he says, emphasizing how the added reach also eliminates the need for a vertical 7th axis lift column, commonly used in smaller cobot palletizers to move the cobot arm up and down: “At 81in, our pallets are a little taller than average, but the UR20 allows us to easily reach the back corners without us having to first elevate the cobot arm with a 7th axis, which would eat into our rate. Now we can just quickly move into position.”
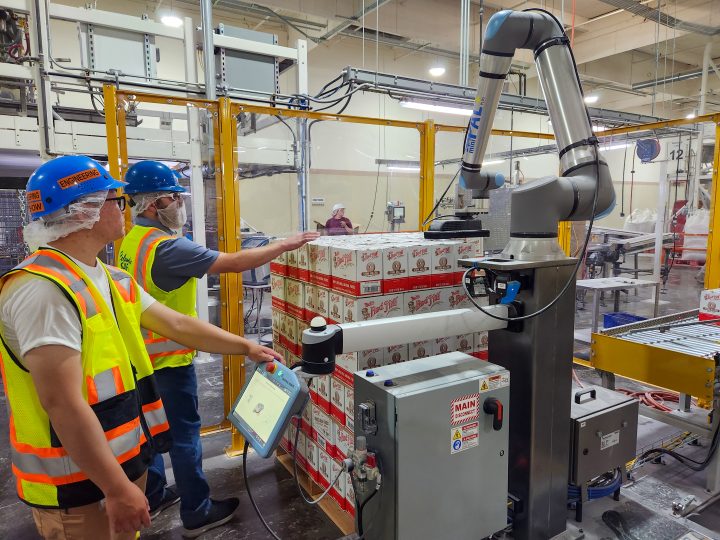
Safety and speed in optimized footprint
The miniPAL® 20 is caged on three sides with a small opening for the infeed conveyor on the back. The wide-open front allows interaction with the cell; whenever a worker or a forklift enters the cobot’s work envelope, the motion is detected by an area scanner that slows the cobot down to 10% speed from 2500mm/second to 250mm/second. In case of collision with the UR20, the cobot’s built-in force and power sensors immediately stop the cobot, preventing injury.
All programming happens though the PALLY software directly on the UR20’s teach pendant. “There are couple of things to learn in terms of pallet pattern design, box sizes, and layouts, but it’s pretty simple and easy to operate,” says Columbia/Okura’s Parker Morris-Pinson, who helped train all four shifts of the maintenance team at Bob’s Red Mill. “It took roughly 45-60 minutes to get us all trained through a multitude of scenarios,” says Nick Chow, who expects to do hundreds of product change-overs with the miniPAL+®.
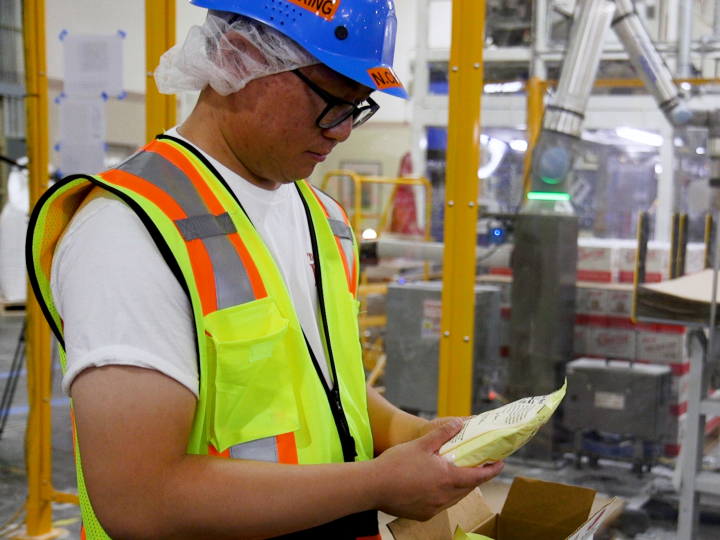
Freed up from ‘boring tasks’
Bob’s Red Mill is employee-owned, a fact that Chow explains has fueled employee acceptance of new technologies: “The employee owners here at Bob’s were really excited to see this palletizing technology come to their production line. If you are producing well, we all get a share of the company profits. Automation is key in helping us grow and share our profits through profit sharing, while also reducing injuries so everybody goes home safely.” The miniPAL® 20 solution has freed up four operators over four shifts in the company’s 24-hour-operation. “Instead of stacking pallets all day long, the operators can now focus on more value-added tasks, such as quality inspection, instead of something that’s boring,” smiles Chow.
Automation challenges solved
- Automating smaller palletizing cells in confined spaces with operator interaction
- Handling high-mix production with numerous change-overs
- Freeing up manual labor from unergonomic hand stacking tasks
Key value drivers
- Extended reach, speed, and payload capacity of the UR20 cobot
- Simple and fast training with user-friendly teach pendant interface
- Ability to reallocate four operators per day for more value-adding tasks
Find out more about Columbia/Okura's collaborative robots
Learn about the miniPAL®