Are collaborative robots the right solution for you?
Fill labor gaps, reduce downtime, and boost productivity with collaborative robots.
Collaborative robots, also known as cobots, are a cost-effective way to improve end-of-line efficiency. They are compatible with multiple product types and packaging applications. Compact cobots are easy to integrate into existing systems, even where space is limited.
Let our experienced team help you determine if collaborative robots are the best solution for your operations.
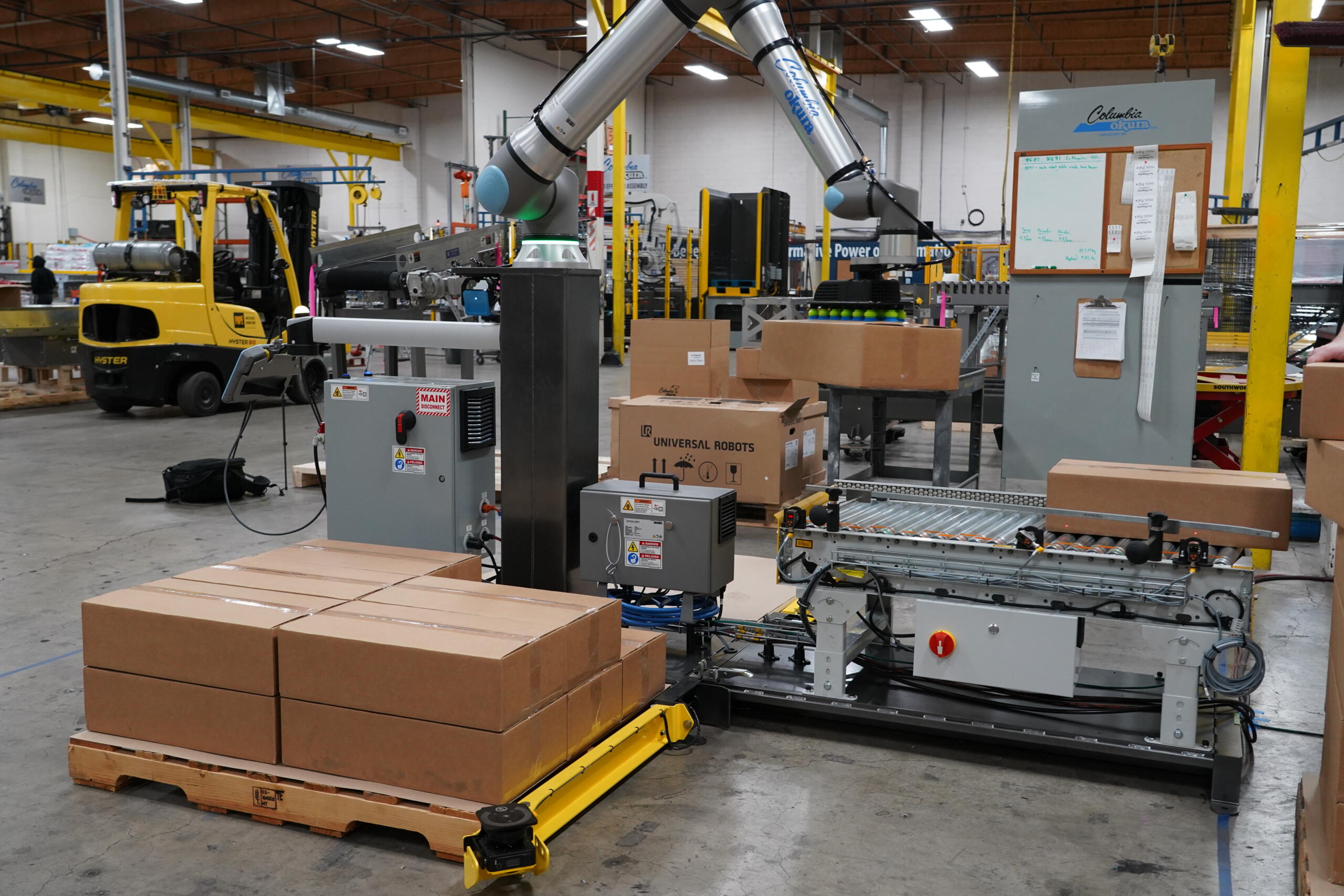
miniPAL®
Since 2019, miniPAL® cobots have been providing our customers with safety, precision, and versatility.
Our miniPAL® cobots can bridge operational gaps and take over high-risk tasks. Easily and safely working in collaboration with employees, they free operators to do other tasks, allowing for higher production without having to hire additional people.
- Applications: cases, spot packs, trays, bundles, and plastic bags
- Equipped with easy-to-use pattern-building software
- Backed by a one-year warranty
Learn about our miniPAL® cobot rental program
Flexible, scalable collaborative palletizing solutions now available for rent
Our miniPAL® cobot rental program provides businesses with access to advanced palletizing technology without the need for significant upfront capital investment.
Find Your Collaborative Palletizer Match
Use the following simulator to get palletizing layouts and suggested cobot solutions for your operations. Simply enter your product’s dimensions, weight, and package orientation. Our software partner, Rocketfarm, will send you a simulation in about an hour. We partner with Rocketfarm to provide the user-friendly software package to program and operate our collaborative palletizing robots.
Custom Cobot Solutions to Meet Your Needs
Showcasing flexibility, innovation, and efficiency, this cobot system was expertly programmed and integrated to transform our customer’s production line. It features three miniPALs®: one for turning boxes, and two for palletizing and placing sheets. Let us design an efficient, cost-effective collaborative palletizing system to optimize your production.
Get Started on Your Growth
Ready to meet your production goals? Let us design a completely integrated end-of-line system that’s right for your business. We’ll even help you develop a comprehensive plan and business case to justify the investment.
About Us
For nearly 30 years, we’ve been helping our customers become more competitive, cost-effective, and productive in a fast-changing world.
Our Partnership Promise
From installation to 24/7 technical trouble-shooting, you’re getting a complete support and service team you can always rely on.
Find answers to common questions about collaborative robot, or cobot, palletizers.
What are cobots and what do they do?
A cobot, or collaborative robot, is a robot intended for direct human-robot interaction and collaboration within a shared space, or where humans and robots are working in close proximity. Cobot applications contrast with traditional industrial robot applications in which robots are isolated from human contact. These collaborative solutions often best service slower production lines that have a constant stream of product that is allowed to palletize over a long period of time.
What factors determine if a collaborative robot palletizer will work for our operations?
Cobot palletizing systems can solve a number of operational problems, such as labor shortages and creating efficiencies to boost production. Your company’s end goal, therefore, is a key factor in selecting the ideal robotic arm. Other considerations include:
- Available floor space
- Packaging type
- Upstream and downstream equipment
- Workflows and processes
How safe are cobots?
Columbia/Okura’s cobots are designed to be as safe as possible. Each comes with built-in force limiting capabilities and multiple levels of safety. Safety scanners and radar actively monitor the cell and control the cobot’s speed. For smaller footprints, guarding provides an extra layer of safety protection.
All of our robots are compliant with ANSI, the U.S. safety standard for regulating the proper use of safety devices integrated with robots and robotic systems. ANSI also provides guidelines for the integration of robots in manufacturing facilities or other work environments.
As with all mechanical systems in production facilities, employers should ensure all employees are properly trained and instructed to follow the operation guidelines provided.